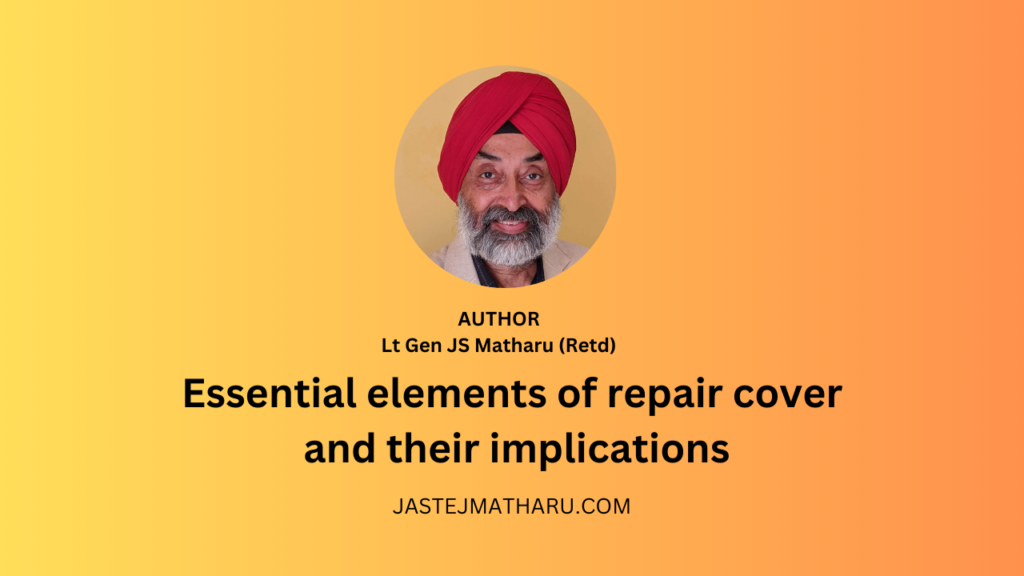
Repair of an equipment can only be carried out if certain elements are present at the point of repair.
The first element is skilled manpower . This person who is there and who has to carry out the repairs must have the knowledge and skills to do what is necessary to repair and bring the equipment back into action. The second element is the spares which need to be replaced. Then you need the test equipment to identify the fault and you need the tools and sometimes special tools which are needed to carry out the repair.
In the case of certain mechanical repairs where complete assemblies have to be changed. It is very important that at the point of repair, we should have the necessary lift so that the assembly can be lifted and replaced.
It should be possible for the person who is carrying out the repair to reach the correct location where the faulty equipment is located.
The repairer must be equipped with the communication so that he or she can connect to backup if needed.
All of this seems quite obvious. However, the degree of difficulty of carrying out a repair will change depending on the scenario under which the repair is being carried out.
If the repair is to be carried out in a workshop where all the facilities are readily available then the only consideration is of the time which is needed to carry out the repair.
On the other hand, if the equipment which has become faulty is located in some far flung area, say in the desert or in the mountains or in jungles, then each one of the activities which were listed become that much more difficult.
The complexity of technology which is needed to carry out the repair is another element. Some repairs are of a nature which cannot be carried out in the field. For example, the repairs to aviation or aerospace equipment. They have to be brought to a hangar where the necessary environment for carrying out such delicate repairs is available. It just cannot be carried out in the field.
Let us take the example of a faulty dozer located in a far flung area.
The mechanical repairs to such dozers need everything including heavy lift capability. If the dozer is repaired in a workshop, it becomes very much simpler, but when it is to be repaired outside in the field under rain or snow, or the desert where it is very hot and dusty, or the jungle where there’s a lot of humidity, then it becomes a much more challenging task.
Even the ability of the repairer to reach the location of the faulty equipment becomes a challenge. The repairer must know how to navigate using maps in difficult areas.
Therefore the nature of repair in the field becomes difficult because of the distance from workshops or from other facilities.
It must be understood that the situation will demand every element to be available. And this may not be easy. For example, the skill which the person possesses must be developed over the years. Next, the person who is to carry out the repair must be available and must be able to reach the location of the equipment and be trained for doing so.
The lift capacity must be available and has to also reach the location for carrying out heavy lift where required. The necessary spares must also be made available.
Each one of the elements must be available. For example the skills, in terms of technical skills and in terms of navigation and use of communication equipment.
These persons have to be trained over the years and the management of the people has to be done so that they are deployed appropriately, especially when a large variety of equipment is deployed in a dispersed manner in the field. A lot of planning has to go into it.
One technician cannot carry out all repairs. So you need specialized technicians. For example different technicians for mechanical repairs, electrical repairs, communication equipment repair, computer systems repair and so on.
Accordingly these people in different trades have to be made available to carry out such a repair.
The training and deployment of the trained manpower is essential for carry out repair of complex equipment deployed in dispersed manner in far flung areas. The process for ensuring this has to be in place.
The test equipment and the tools they have, also must be planned for and this has to be done in detail so that they are available when needed.
Then comes the issue of spares. Now, this is a much more difficult thing to prepare for. The supply chain of these pairs has to be planned in great detail.
Let us look at the stocking levels of spares at various levels needed to ensure in time availability of the correct spare in a remote location.
This is very difficult to predict.
Take the case of a dozer. Dozers may be purchased by an organization in a certain quantity in a particular year. The particular equipment model is going to change and it’s not going to be available after some time even though it has to be utilized for a prolonged period of time.
Then the question arises how much of the spares have to be purchased in advance? and how will they be stocked? This may be quite costly as well.
Planning for the life cycle spares of the equipment may restrict the number of equipment you can procure due to cost constraints.
Therefore contracting for such equipment becomes complex.
In the case of defense equipment, let us say tanks or radar systems or other complex equipment, this becomes an even a much more challenging task.
Should we go in for a lifetime purchase of spares? Or should we go in for a certain lesser number of spares and get the remaining on an as required basis?
These issues are difficult to answer.
And the biggest problem here is the aspect of cost.
If the supply chain fails then you have to resort to cannibalization and at times write off certain numbers of the equipment to keep the remaining functional.
Many times you have to do innovative repairs, or you create spares locally even if they may not be of the required quality.
The issue of not being able to get the spares can become a major factor towards reducing the availability of equipment.
Sometimes there is a tendency to over-stock, especially if the equipment has a long lifecycle.
It all depends on the criticality of the equipment.
Obviously, in the case of defense equipment, the criticality is very high. So there is a chance that we may land up overstocking. But then again, if we do not do the overstocking then we will have to do without the equipment when it is most critical and when it is needed in a crisis.
These questions are very difficult to decide upon. Nobody knows what is going to happen tomorrow. Conflicts can arise out of nowhere, and these questions need to be answered.
Right to repair is being talked about these days. This is an important concept to keep in mind. The OEM may insist that the spares are available only from them. But when we sign such contracts it is important that you consider a clause which comes into effect in the event of failure of the spares supply chain.
The user must be fully empowered to go in for the replacement locally or from some other sources and also be empowered to reengineer.
While mechanical components are easier to re-engineer, it is difficult to do so with electronic equipment. And it becomes even more difficult for software.
When an equipment uses embedded software it must be contracted that, in case there is a failure in the supply chain and the software is no longer made available by the OEM then the user of the equipment may create such software themselves.
The specifics of the inputs to particular assembly and the outputs must be clearly known and allowed to be replicated.
We are bound by certain procedures while procuring items for the lifetime of the equipment. At times the problem with this is that the procedures are generic in nature. They apply across the board for many types of purchases. And they may not necessarily suit the purchase of a particular complex equipment.
More bespoke solutions, therefore, need to be found in such cases.
For example, if we have equipment which is deployed in the hinterland, which does not need to be taken forward. There we could follow the performance based logistics or the PBL approach. And as a result hold very little spares and periodically test the equipment. And depending on the analysis and based on condition monitoring, we are able to decide what is needed and we are able to bring in the item.
But this is not possible in the case of equipment which is deployed in the field in far flung areas. There, we have to buy spares in bulk and keep them. This adds to the cost and to the deciding of how much equipment can be procured.
In such situations the time taken to repair due to non-availability of spares becomes a factor. When you are unable to provide such spares in time then the downtime of the equipment starts going up.
And especially in the case of defense equipment, which is needed then and there to operate in a crisis; this luxury of time just does not exist. This must be considered while planning to procure spares for such equipment.
Some repairs need specialized processes and the OEM may put restrictions on those repairs being carried out only in their facilities.
Such a clause in the contract has to be looked at very carefully because if the equipment has to be withdrawn from the field and taken back to the OEM, then the turnaround time of the equipment becomes too high and the equipment may not be able to return in the time needed to be utilized. Thus negating the need for which the equipment was procured in the first place.
Therefore, aspects of turnaround time also have to be considered and it should be thought out very carefully as to where and what facilities you create in the field or closer to the field so that you keep the turnaround time of repairs of critical equipment as low as possible.
This is easier said than done, because in the desire to reduce turnaround time the cost starts going up so there is no easy solution to this.
So if you are able to create a flexible solution where every possible option is available to the purchaser of the equipment and the purchaser is able to exercise those options at times of crisis.
Options like going for alternative spares, the re-engineering options, getting certain transfer of technology from the OEM at the time of contract so that people can be trained for it. All these options have to be looked at very carefully.
Especially in the case of defense equipment, this is critical because they tend to be used for a much longer time than initially thought of. For example, typically a tank even if it is 30 to 40 years old may be upgraded and its life extended to 50 years or more.
Does one go for a lifecycle contract or to go for the best technical equipment or to go for the cheapest equipment? What equipment is on offer? All these questions have to be looked at very carefully.
A collective procurement solution by everybody involved must be found. That is the person who needs the equipment, the person who looks at the finances, the person who will look at the training of the technicians and the spares, all these people have to sit down together and on an equipment to equipment basis, come out with a solution.
They must be empowered to make decisions even if the procedure needs to be changed for every equipment.
The aim of this article is to give an overall picture and to show that it is very important that each one of these elements, the element of training, the element of tools and special equipment, the element of spares, the management of lift equipment, the management of communication, the training for navigation, each one of these elements is ensured.
Only then and only then you will be able to deliver at the point where the repair is needed.
And this is most crucial in the case of dispersed and remotely deployed defense land systems.