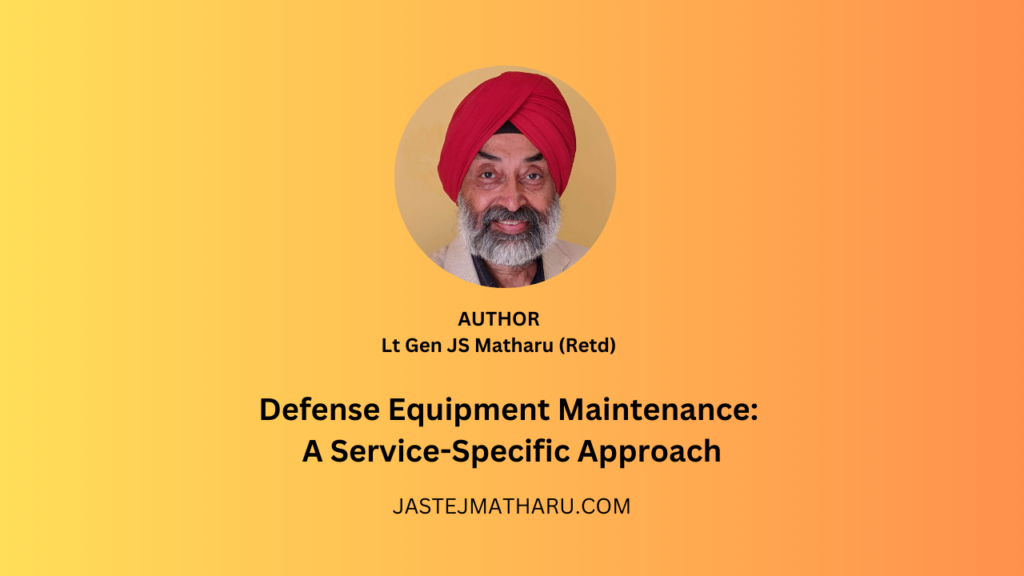
The maintenance of defense equipment is essential to military operations, but the approach differs significantly across branches. Each service—the Army, Navy, and Air Force—tailors maintenance processes to its unique operational needs, environment, and equipment, while sharing fundamental principles aimed at minimizing downtime and maximizing equipment longevity. This article explores the core elements of defense maintenance, its branch-specific variations, and common pitfalls, underscoring the need for well-trained personnel and strategic planning.
Core Elements of Maintenance
The primary aim of maintenance in defense is to ensure optimal equipment functionality, minimize downtime, and extend the lifespan of assets. Achieving these objectives involves several maintenance strategies:
Preventive Maintenance:
Routine inspections and scheduled services prevent unexpected breakdowns.
Predictive Maintenance:
Leveraging sensor data, thermal imaging, and condition monitoring, predictive maintenance aims to address potential failures before they occur.
Corrective Maintenance:
Reactive repairs are made when equipment has already broken down. This tends to be costly and is typically a last resort.
Reliability-Centered Maintenance (RCM):
This strategic approach assesses failures to develop the most efficient maintenance methods for specific equipment.
Computerized Maintenance Management Systems (CMMS):
CMMS software assists with work order management, inventory control, and asset tracking, streamlining scheduling, record-keeping, and reporting.
Root Cause Analysis:
Identifying the underlying reasons for equipment failures enables targeted solutions, which reduces future issues.
Inventory and Spare Part Management:
Efficient spare part management ensures the availability of necessary parts, which involves tracking usage, reordering cycles, and storage.
Documentation and Record-Keeping:
Maintenance records such as inspection reports and repair logs aid in trend analysis, regulatory compliance, and informed decision-making.
Training and Skill Development:
Training personnel is critical, as skilled maintainers are essential for both new and legacy systems.
Safety Protocols:
Ensuring adherence to safety standards is paramount during all maintenance activities.
Together, these components form a proactive maintenance framework that enhances reliability, minimizes unplanned downtime, and optimizes resources.
Army, Navy, and Air Force: Service-Specific Maintenance
Each branch has a distinct maintenance strategy shaped by its operational environment and asset deployment.
Army Maintenance: Mobility and Flexibility
Army equipment operates in diverse terrains, from deserts to high altitudes, enduring harsh conditions such as dust, mud, and extreme temperatures. Given the Army’s expansive deployment areas, maintenance must be highly mobile. On-site repairs are often necessary, supported by mobile repair teams and field workshops that move with front-line troops.
Skilled manpower is essential for the Army, as maintenance personnel are often deployed in remote locations where logistical support may be limited. Maintenance teams must be carefully composed with the right skills, tools, and spare parts, as reallocation is challenging once deployed. Preventive maintenance, including daily and weekly checks, is prioritized, as is retraining to ensure a young, physically capable workforce ready for deployment in high-stress environments.
Navy Maintenance: Self-Reliance and Corrosion Prevention
Naval systems are designed for long-term operations at sea, where maintenance focuses on preventing corrosion. Unlike Army teams spread across vast areas, naval personnel remain collectively on board, simplifying coordination. Spares are carried onboard, but careful planning is required to avoid overstocking.
While ships perform regular maintenance at sea, major repairs and upgrades occur at shipyards or naval bases. Redundant systems are built into ship designs, ensuring resilience during extended deployments. As with the Army, ongoing training is crucial, with the added emphasis on corrosion management and redundancy.
Air Force Maintenance: Precision and Safety
Airborne systems necessitate a highly specialized maintenance approach due to their complexity and the high-risk nature of aviation. Maintenance personnel, stationed at air bases, undergo intensive training to ensure precision repairs. Aircraft undergo rigorous pre- and post-flight inspections, with meticulous documentation to avoid any lapse in safety standards.
The Air Force benefits from centralized spares storage at air bases, though forward bases require readily available spare parts for operational efficiency. Precision is paramount, and maintenance protocols are stringent, especially for avionics, communication, and navigation systems.
Maintenance Cycles, Complexity, and Logistics
Maintenance Cycles:
The Army’s maintenance schedules are flexible and mission-dependent, with frequent spot checks. The Navy adheres to a rigorous, planned schedule, aligning maintenance with docking cycles. The Air Force conducts regular checks pre- and post-flight, with extensive inspections during downtime.
Complexity and Skills:
Army personnel need the agility and expertise to perform maintenance under field conditions. Navy personnel rely on onboard specialization, while Air Force personnel require advanced technical training for high-precision tasks.
Logistics and Supply Chain:
Army spares are distributed for mobility, while the Navy’s spares are stored onboard and carefully managed. The Air Force centralizes spares at bases but requires rapid access at forward bases.
Common Pitfalls in Defense Maintenance
Each branch faces unique maintenance challenges, yet some issues are universal across the services:
Neglect of Preventive Maintenance:
Skipping preventive checks increases the likelihood of equipment failure during critical moments.
Corrosion:
The Navy faces a heightened risk from corrosion; regular anti-corrosion treatments are necessary to prevent premature degradation.
Documentation:
Incomplete records or poor documentation can lead to missed inspections, safety hazards, and regulatory issues, particularly in the Air Force, where every detail is crucial.
Cybersecurity Vulnerabilities:
As military equipment becomes increasingly digitized, securing maintenance systems and digital controls against cyber threats is essential.
Training and Skill Development:
Inadequately trained personnel can compromise safety and performance, making consistent training essential.
Communication and Coordination:
Misalignment in resource allocation and poor communication can severely hinder maintenance, particularly for Army and Navy field operations.
The Role of the Maintainer: Continuous Training and Experience Transfer
At the core of all defense maintenance is the “maintainer.” Unlike civilian industries, where service stations or fixed industrial facilities offer support, the Armed Forces operate in dynamic environments with young personnel who must be capable of maintaining equipment independently in the field.
One approach to addressing this challenge is rotating young field personnel to maintenance depots periodically. Here, they can work alongside experienced maintainers, gaining hands-on knowledge and nuances that only experienced personnel can impart. When these young maintainers return to the field, they bring invaluable skills and confidence, critical for operational success under pressure.
Conclusion
Military maintenance is integral to operational readiness, safety, and longevity of equipment, demanding a blend of technical expertise, rigorous planning, and adaptability to branch-specific needs. By investing in skilled manpower, tailoring strategies to each service’s operational demands, and continually refining training, defense maintenance planners can ensure mission-critical equipment performs reliably—even in the most challenging conditions.